A few years ago i bought a 24mm f/2 vivitar lens for something like 15 euros, the price was too good to not buy it. It was laying around pretty much untouched until a few days ago
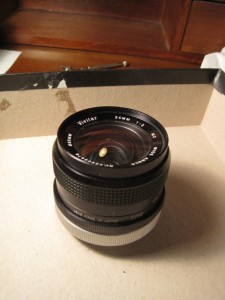
It has a Canon FD mount, which means it is compatible with all Canon FD cameras. Sadly iam not a big fan of these cameras, I like conveniently working manual mode and digital. Adapters for FD->EOS exist but they require optical elements to compensate the otherwise negative adapter thickness that would be needed. So a more geeky solution is needed. But first problem with it is, its aperture is stuck and full of oil
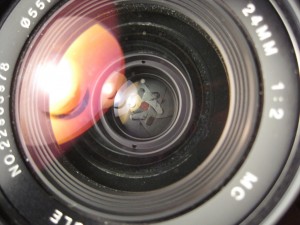
Now cleaning an aperture is not hard, though do NOT try it with this lens if its your first such repair attempt, as this lens is a floating element design, which in laymen terms means complex. The tools you need are just a bunch of small screwdrivers (for most screws the cheapest will do), some paper towels for various things, a clean soft brush to remove dust. And something to clean the aperture blades, probably anything that removes oil would do. And a box of some kind to put all parts in when taking them apart so tiny things are trapped by gravity inside a quickly search-able space and not your whole room. First step is to loosen the screw on the side of the front

After that the top can be unscrewed, the next part is hold in place by a similar screw, loosen it too and unscrew the part, be careful as this exposes the front glass element and if you take it out, only thing you will achieve is getting dust in.
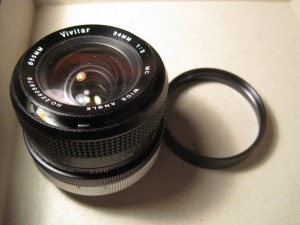
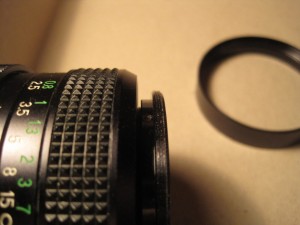
Now you need to remove the 2 screws and the part that holds the front lens group in correct distance/rotational alignment, you do want to take some notes or add markings to get it later back in exactly the same position. As i am lazy i relied on my carefully composed pic above instead of wimpy notes or markings. You also need a good screw driver here as these screws arent easy to loosen even after removing the stuff that holds them in place with aceton. After you removed the 2 screws and that thingy, put the ring that held the front element in place back so the element doesnt escape
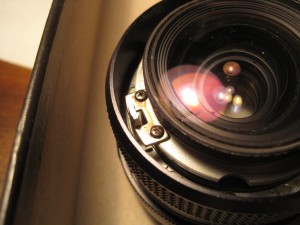
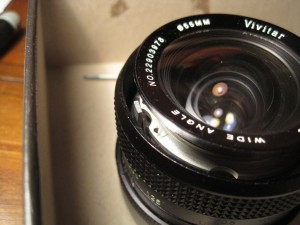
Once the glass is secured you unscrew the front group as a whole (you have to turn it in the other direction from what you expect). After unscrewing it you reach the front side of the aperture. And here i believed i could just remove the 3 screws and take it out, but no its not nearly so easy.
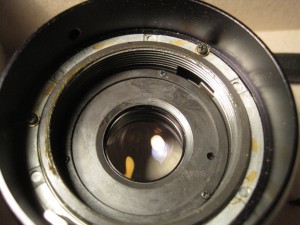
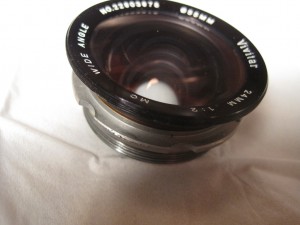
So as we cant get it out yet, disassembling of the bottom is next, remove the 3 screws that hold the mount in place, beware there is a spring, a small pin and a metal ring that are more or less loose
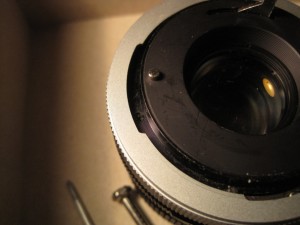
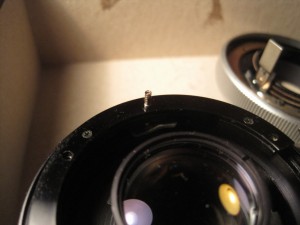
The rear lens group is just screwed in and can easily be screwed out, allowing us access to the rear part of the aperture, what the annoying part is we still cannot take it out for proper cleaning.
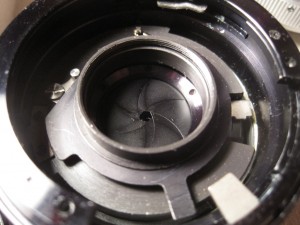
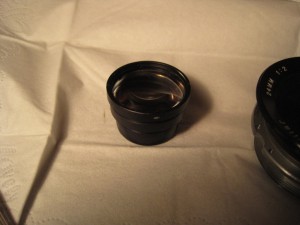
To move forward next step is to remove the 2 screws and the part that hold the inner rear part in distance and rotational alignment, again take notes and make markings, the rear part is a little fiddly to put back together with markings (aka expect 2-3 minutes for doing that later) without markings, it would probably be fun but not impossible.

Now the inner rear can be screwed out. And hidden you will find 3 holes in the helix, in these holes there are screws that hold the aperture in place, to loosen them take careful note of their original position, or just be lazy and do like I and do exactly 3 full turns, so you can get it back with 3 exact full turns later. It shouldnt ruin the lens if the aperture isnt centered exactly but id guess there was a reason for this odd way to mount it
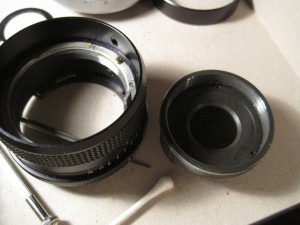
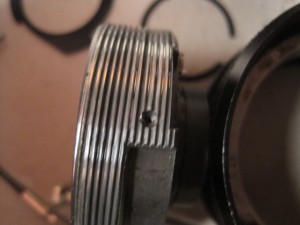
Once the 3 screws are loosened a bit (and a spring is removed) the aperture can be taken out, its further disassembly and reassembly should be obvious. To clean it you can probably use almost anything, i used a little window cleaner in a small container put all parts in and used the “shaken but not stirred” technique, in addition cotton buds and 100% ethanol. Note the pictures below dont look so oily because I tried cleaning it before full disassembly with cotton buds
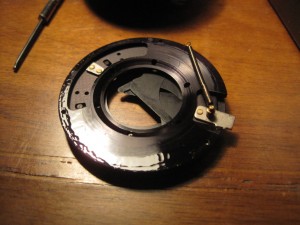
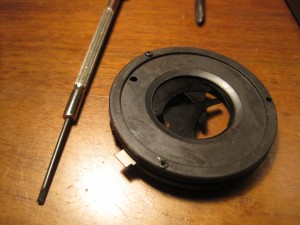
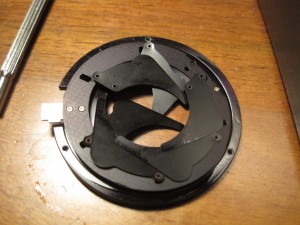

Once cleaned, reassemble everything, its trivial just reverse of disassembly
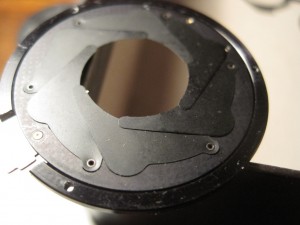
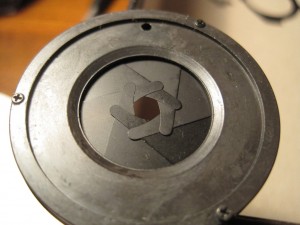
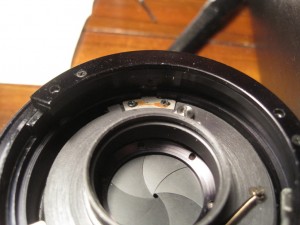
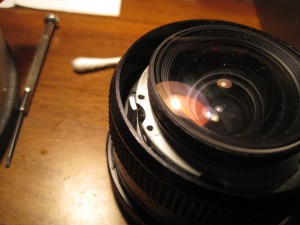
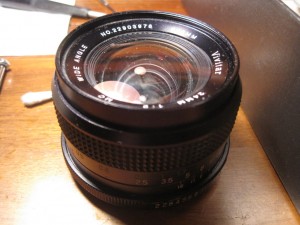
From FD to M42 to EOS
The rear FD mount was kept in place by 3 screws, looking a bit around i found a worthless 35mm/2.8 M42 lens laying around that only produces blurry images no matter what, though it was in 100% perfect condition, surely used only once by any previous owner. Its rear fits almost, 2 out of 3 screws can be screwed in without modification. For all 3 a little drilling is needed
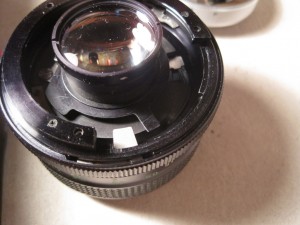
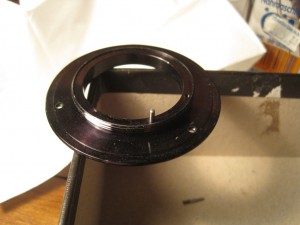
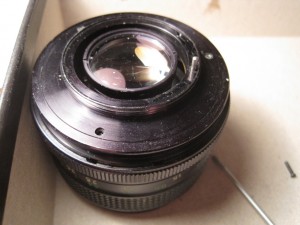
With this hack it can be mounted on any M42 camera or with M42-EOS adapter on any canon EOS DSLR. it doesnt focus beyond 1m in that configuration though. That is at 1m real distance you are at infinite on the scale. Also its easy to switch the mounts back :)
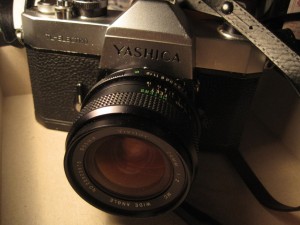
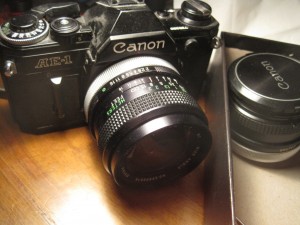
Now to get it focus to infinity we need to loose some material, first the M42 rear i picked had a circular ridge that screamed to me “flatten me”
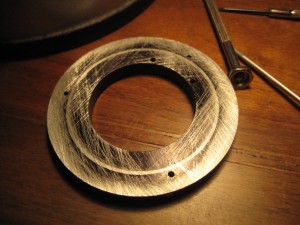
The pic above shows it in the middle of the flattening process. This wasnt enough though, infinity focus still was far away, so the ring that keeps the aperture selection ring in place had to go too. Note, below the next (now loose) ring are 2 loose springs and 2 tiny steel balls dont loose them if you try this. A magnet is a pretty nice way to temporary store them safely.
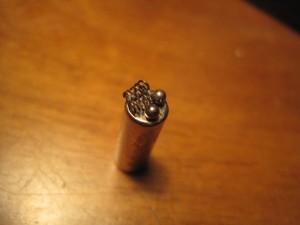
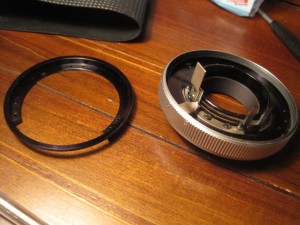
With this ring too removed infinite focus becomes possible on M42 and EOS. But due to all the removals, one ring holding the aperture selection ring in place and the aperture controlling parts that where part of the FD mount. We still arent done, so next is rebuilding the aperture control parts that a manual lens would have. Ive build it out of a piece of aluminum that i found in a old box from my grandfather, I still remember how my mother wanted to throw all the stuff from him away, lucky i safed a few boxes…
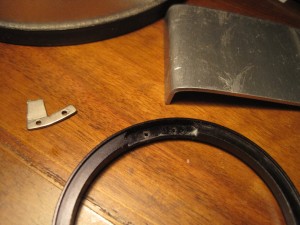
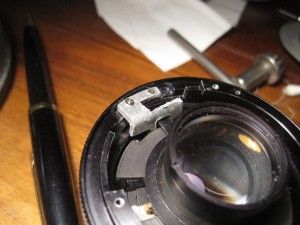
Above picture shows it in partly finished state, it needed more filing and bending before it worked fully smoothly. The removed ring also needs to be replaced. One could have just made it thinner but i dont have the tools to do this exactly and quickly, besides it would make it impossibly to undo it. So i used a piece of plastic cut from a cap of something random from the bathroom, also to get the focus a bit closer to correct (it was way over infinity) i put the thin metal ring from the FD mount back in
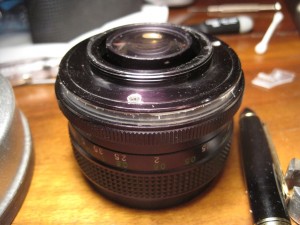
And last fine-tuned the focus with the 3 screws intended for that purpose visible at an earlier picture, cleaned the glass a bit and ready is my 24mm f/2 vivitar/kiron for M42 and EOS.
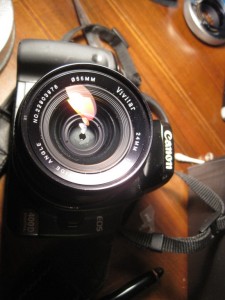
Was the work worth it? For the lens/photography, probably not. For the fun and geek factor, absolutely yes. :)